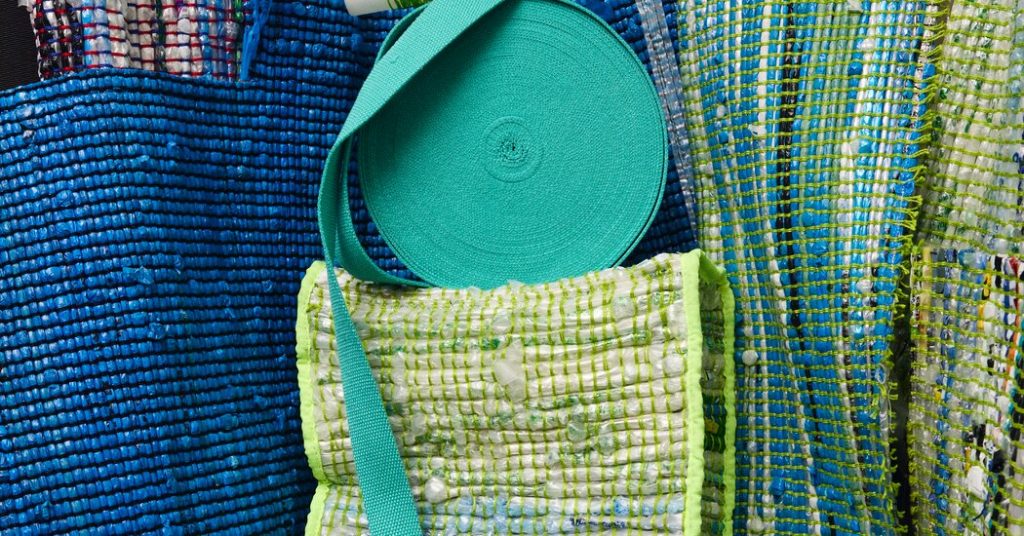
Not Just Any Bag
This article is part of a series examining Responsible Fashion, and innovative efforts to address issues facing the fashion industry.
“Plastic is not going anywhere anytime soon,” said Alex Dabagh, who started the company Anybag, its name a play on the ubiquity of plastic bags and an ode to his hometown, New York City, two years ago.
In kitchens the world over, often there is a cabinet or pantry door hiding a plastic bag stuffed with other plastic bags. And behind the doors of Mr. Dabagh’s office in the Chelsea neighborhood is a factory that makes plastic bags — totes in different sizes — woven from plastic bags like these.
The staggering sight of all the single-use plastic bags that came through the doors of his primary business, Park Avenue International, a 6,000-square-foot leather goods factory that specializes in producing handbags for brands including Gabriela Hearst, Altuzarra, Proenza Schouler and Eileen Fisher, became too much.
“I was like, we’ve got to do something with it, there’s got to be a better way,” Mr. Dabagh, 40, said. “If we can weave leather, there’s got to be a way to weave plastic.”
He broke down the bags, heat sealed them into long strands — just like a typical textile — cued them up on one of his massive looms and, after a few months of trial and error, came up with the Anybag prototype that was shown at ReFashion Week NYC in February 2020, which was within weeks of New York State’s plastic bag ban.
Mr. Dabagh, like many New Yorkers, knows that despite the ban, there are still plenty of plastic bags in circulation and that the recycling system is murky when it comes to them. “The recycling companies don’t want them because all they do is clog their machines, cause millions of dollars in damages every year — stoppage time, broken machines, clogging the incinerators.”
At the beginning of Anybag, he was sourcing from friends and family, asking them to bring in their plastic bags. His mother struck up a deal with a local supermarket in the Bay Ridge section of Brooklyn to collect its bags. He started calling local Home Depots and CVS branches — businesses on which the plastic bag ban was enforced — to get their dead stock bags, and he formed partnerships with local schools to collect bags that are left in drop-off bins.
Mr. Dabagh estimated that last year Anybag collected 12,000 pounds of plastic, the equivalent of about 588,000 single-use plastic bags. The company strips everything down, cleans it and disinfects it.
“It’s crazy how much virgin plastic we get in here from shipping companies, packaging companies or a demo company,” Mr. Dabagh said. “They’ll go into a building to clean it out and be like, ‘We just found these boxes and piles of plastic that haven’t been separated. Do you want them?’ I’m like, ‘I’ll take it, that’s gold.’”
A sustainable mind-set was instilled in Mr. Dabagh by his father from a young age. Pierre Dabagh opened Park Avenue International in 1982 as a young immigrant who had fled Lebanon in the late 1970s during the country’s civil war. He arrived in New York with $300 and started working at a factory owned by a Korean family on 30th Street, Mr. Dabagh said, where he learned the leather trade before opening his own shop.
Well aware that the leather industry has a less than pristine reputation when it comes to sustainability, Mr. Dabagh said that his company works with Italian tanneries that adhere to strict regulations and use leather that is purely byproduct. All of the leather scraps at Park Avenue International are collected and repurposed for reinforcement, backing and bonding in the company’s wares.
“Every shelf has scraps of leather that we just collect,” Mr. Dabagh said. “We don’t throw anything out. It’s something I learned from my father. He was like, ‘This is all worth money. There is value behind everything.’”
At the start of the pandemic, when Park Avenue International’s core leather business slowed down, Mr. Dabagh decided to double down on Anybag. He trained his 40 employees to use the looms to weave plastic bags out of trash instead of leather goods. “I was like, ‘We’re going to try this out.’ They all thought I was crazy.”
Two years later, Anybag is roughly 10 percent of Park Avenue International’s business. Mr. Dabagh said that revenue from the bags tripled in the last year. He acquired a new loom devoted only to weaving plastic for Anybag, and is developing automated looms that will allow him to quadruple output and cut costs.
His staff can weave five to seven yards of plastic a day, which makes about 20 totes. Each bag is sturdy, with a crinkly texture that can hold up to 100 pounds. They’re trimmed in colorful canvas with straps in pink, fluorescent yellow, royal blue and black. The bags come with a lifetime guarantee — the plastic will outlive us, after all — and free repairs.
The bags are sold through the company’s website. There are three styles, the Classic, the Mini and the Weekender, ranging in price from $98 to $248. The Classic and Mini are shaped like typical shopping totes; the Weekender is akin to Ikea’s well-known Frakta shopper. Mr. Dabagh has teamed with Adidas, Ralph Lauren, Beyond Meat and Miranda Kerr’s cosmetics line, Kora Organics, customizing bags for media events and for the brands’ own internal use. But for the most part, a typical Anybag is made from whatever is around — plastic from packages of Bounty, Cottonelle or bags used to wrap DHL shipments or copies of The New York Times.
“We’re slowly realizing we’re a recycling company,” Mr. Dabagh said. With more investment, he sees an opportunity to scale up and develop hubs around New York City, and eventually the country. But for now, Anybag is a proudly local operation.
As Mr. Dabagh said, “It’s all handmade, handcrafted by New Yorkers, in New York, using New York City’s finest trash.”